I Hope You’re Sitting Down
Dust Collection System Design
Don’t Miss Real-World Variables
Calculating and engineering of Dust Collection systems is critical to their success and safety, but when does engineering miss real-world factors? More importantly, how can we deal with these real-world considerations and still maintain desired results and effective control? The answers to this dilemma are not a one size fits all approach.
In an effort to save horsepower/energy many dust collection systems have been designed at or near the minimum conveying velocity of the particular dust. Too often not enough pressure drop is figured across dirty filters. This may be fine for the first week or so of a system but soon the pressure drop exceeds the allowance and ducts quickly start to experience buildup leading to poor collection of dust in the workspace and an accumulation of combustible materials in the ductwork.
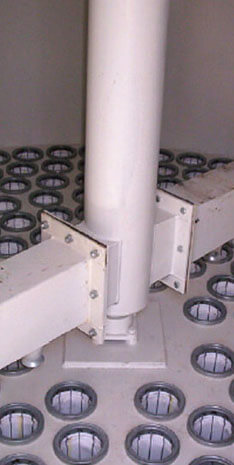
The use of dampers, blast gates and valves for control of air flow is not only necessary but also demanded in NFPA Guidelines, yet their misuse creates problems leading to dangerous conditions especially when collecting combustible dusts.
Duct sizing and routing that does not account for process equipment usage, work flow and potential washdowns can be heading for insufficient airflow which can create conditions hazardous to the health of those in the workplace. High duct velocities can lead to rapid wear and failure of duct systems exposing personnel to levels of dust above acceptable limits.
It is a certainty that not everything that could happen can always be anticipated during the engineering process of any system no matter how hard one tries. Steps can, however, be taken to either alert personnel of out of design conditions or even to anticipate and correct such conditions through automation. Lack of proper procedural controls also lead to system issues.
Addition of monitoring and/or control equipment into a dust collection system usually represents a small addition to the overall price of the installation but can yield significant ongoing cost savings related to system performance, maintenance and production line down time. Health and safety conditions are usually enhanced as the air in the workspace is cleaner. Information needed to make the decisions on what steps to take and how to apply them can largely be determined in engineering books and calculations however, there is also tremendous value in taking the time to observe the processes, the hiccups and upset conditions and when possible to get input from the operators on the floor who are usually those most affected by the system’s operation.